A Comparison of Conductive Coatings for EMI Shielding Applications, Part II
The second part of the series A Comparison of Conductive Coatings for EMI Shielding Applications will discuss Conductive Paints for EMI Shielding Applications.
Conductive paints have traditionally been used to coat plastics to achieve EMI shielding. This technology is based on the incorporation of a conductive filler and pigments into a resin binder. In general, the alternative types of conductive fillers used in today's conductive paints include copper, silver, graphite or nickel. The primary binder systems used in the formulation of these products include vinyls, acrylics, polyurethanes and epoxies.
Paint Types
The most commercially significant conductive paint technology today is based upon copper. This may or may not include the use of silver–plated copper fillers to enhance copper conductivity and to assist in protecting the copper film from oxidation when exposed to corrosive conditions. Conductive copper and silver paints are primarily suited for addressing the requirements for shielding in the E–field and plane wave applications. They possess no significant capability to provide H–field shielding. Permeable materials like mumetal are best suited for these situations.
Silver–based conductive paints offer excellent conductivity and can be applied at lower dry film thicknesses while still providing effective shielding. However, the very high material costs associated with silver paint tend to restrict its use.
Nickel conductive paint has been a traditional shielding choice for plastic parts, but its lower level of conductivity has begun to limit its use for many of today's electronic products. Although the performance of nickel paint, in most applications, is not equal to that of copper paint, electroless plating or vacuum metallizing, it continues to meet the needs of the market when shielding requirements are more modest and the environmental resistance of the coating is not a significant issue. One advantage of nickel paint over copper or silver paint is its durability, due to the hardness of the nickel. In addition, as is the case with greater thicknesses of plated nickel, limited amounts of Hfield shielding can be attained when nickel paint is used.
Paint Application Techniques
Conductive paints usually involve high solids, solvent–borne processes, although some waterborne processes are also used commercially. The paints themselves are applied through a variety of conventional spray techniques, and as such, can be processed at a number of commercial operations. High–volume, low–pressure (HVLP) equipment is most often selected for conventional spraying operations. HVLP equipment improves the transfer efficiency of the paint as compared to traditional high–pressure spray equipment (air atomizing or airless). Typical over–spray losses for conductive paints are in the range of 30 to 40 percent. For parts with less complex geometries, over–spray losses can be less than 30 percent. In contrast, with more complexity incorporated into the designed–in features, additional passes are necessary to avoid flooding in some areas and/or leaving voids in others. Thus, over–spray losses tend to increase under these circumstances. In high–volume production, robotics and HVLP equipment are employed to improve uniformity and consistency in the application of the paint.
Conductive paints, by the very nature of the process, are selective to the areas where they are applied. As such, they use masking techniques similar to those employed for selective plating. The shielding performance of the conductive paints varies with the thickness of the dry paint film and with the inherent conductivity of the paint, which is a result of the filler used and the uniformity of the conductive filler within the binder system. Surface resistivity is also influenced in the same way and is further affected by variations in the uniformity of the paint film over the entire surface of the part. In cases where the paint is flooded onto the part, settling of the conductive fillers in the paint film may result, reducing conductivity in that area.
Typical thicknesses used to achieve adequate EMI shielding from conductive paints are summarized in Table 4
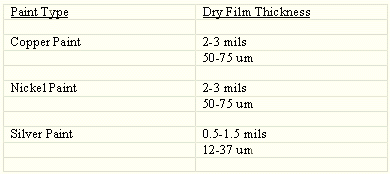
The past two weeks we have learned about electroless plating and conductive coatings for EMI shielding. Next week, we'll explore vacuum metallizing as well as some of the conductivity testing used in these applications.
By Edwin Bastenbeck, Brian Jackson, Peter Kuzyk and Gary Shawhan of Enthone-OMI
Seleco, Inc., 8427 Zionsville Road, PO Box 68809, Indianapolis, IN 46268 Phone: (317) 872-4148 Fax: (317) 875-3276.