Aerospace/Airline Plating & Metal Finishing Forum: Barrel Plating Innovation Simplifies the Electroplating Process
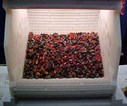
Barrel plating is a tried and true technology that has been around for years. However, Technic, Inc. (Pawtucket, RI), has come up with a new advancement in barrel plating technology that is sure to save platers significant time and money.
The TumblePlater eliminates the need to transfer an entire barrel from station to station. Via the patented Low Impact Transfer (LIT)-design moving belt that is able to stand up to aggressive solutions, the parts are moved from station to station in a gentle fashion while also cushioning the parts being plated. In addition, delicate parts that previously could only be rack plated, can be barrel plated using the TumblePlater technology.
Another advantage of this barrel plating technology is the fact that dragout has decreased by 70% to 90% by volume over conventional barrel plating because only the parts are being transferred from station to station, not the barrel. Thus, the solution that normally clings to barrels is left behind. According to the manufacturer, applications requiring higher temperatures can make use of special in-station fog or spray nozzles that rinse the parts at each station, further reducing dragout.
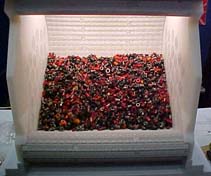
Plating time is reduced 30% to 50% because there is a direct line of current between the parts being electroplated and the anodes; the barrel walls are torn down. The direct line of current and rolling approach also lend themselves to more even surface plating.
The TumbleDryer allows in-line drying. The heat injectors are mounted on the top of the enclosed unit. Even blind hole parts can be dried in-line successfully. In-line drying eliminates the need to move parts to a secondary drying operation, saving space and labor-intensive material handling. The system can take parts directly from totes and deposit the plated and dried parts back into totes at the end of the line.
Station enclosures are available to remove fumes from the process area. According to company representatives, this also reduces waste treatment and labor fatigue as well as costs. The system is fully automated using the company's Windows-based software and PLC controls.
For those who doubt the abilities of the TumblePlater, Technic operates two beta units – one on the East Coast and one on the West Coast. Each unit is a two-station unit that platers can use for up to 30 days. All they have to do is pay for shipping of the unit. If they are satisfied with the final results, platers can then purchase the system. Perhaps another testament to the system's operation is the fact that Technic has already spent a significant amount of money fulfilling two major orders for zinc applications.
For more information, contact Technic, Inc., 55 Maryland Ave., Pawtucket, RI 02860. Phone (401) 728-7081; Fax (401) 722-1720, equipment@technic.com.