Brush Plating - Taking the Plating Process to the Part
By Derek Vanek
Sifco Selective Plating, Division of SIFCO Industries, Inc., Cleveland, Ohio
Most of the metal finishing activities we're familiar with are accomplished by bringing the part to the process. Sometimes, unfortunately, the part is just too big to move or too difficult and time consuming to disassemble… so the process has to be brought to the part.
Brush plating is a portable electrochemical process that is used to electroplate, anodize, and electropolish localized areas on both OEM components and parts that need deposits for repair and dimensional restoration.
Why Use Brush Plating?
Flexibility and versatility. You can use this portable process virtually anywhere in the shop or out in the field. It can be taken right to the jobsite to perform operations such as plating nickel onto localized areas of the international space station, touching up defective cadmium on aircraft landing gear, resizing worn stamping equipment crankshaft bearing diameters, and repairing scores and pits in valve stems at nuclear power plants.
Save time and money. Because you can take the process to the part, you can eliminate the shipping costs and reduce the turnaround time to have a completed part. You are not at the mercy of the tank plater's schedule. Additionally, you can minimize the disassembly / reassembly - you may not have to take the part out of the system in order to apply the coating or deposit.
Other methods will not work. Brush plating offers several advantages over it's biggest competitors - tank plating, flame spray, and welding: Masking is minimized - Extensive masking is required in order to plate or anodize a localized area on a large component in a tank. Brush plating requires only minimal masking of the area adjacent of that to be plated, thus reducing processing time. Quite often parts are even physically too large to fit into a tank. No heat is involved - Both flame spray and welding operations develop tremendous amounts of heat that can distort the part. Brush plating and anodizing do not - and because of the ability to accurately control deposit thickness finish machining or grinding operations are not always needed. In many cases, parts can be plated right to the desired thickness and then put into service!
Case History
During a routine maintenance operation on a Mann Roland Printing Press, a 1/8" allen wrench fell between the plate and blanket cylinders leaving an impression in each cylinder that was approximately 0.050" deep.
The initial repair option was to completely remove both cylinders and have them ground undersize, chrome plated, and then reground to achieve the desired finish and dimension. The turn time was estimated at a very costly six days.
Brush plating provided an alternative that required no disassembly. The portable plating equipment was brought right to the press. The cylinders were indexed to provide easy access to the defects for plating. And with minimal masking to isolate the areas to be plated, the defect in each cylinder was filled with several layers of copper and then hand dressed slightly undersize to allow for a final cap of cobalt. The repaired defect area in each cylinder was then polished by hand to achieve the desired finish, and was well within the 0.001" allowable tolerance for the diameter.
Copper was chosen as the fill material of choice for two main reasons. First, because of its ability to plate efficiently at the bottom of a deep defect (throwing power). And second, because it is easy to work by hand (i.e., filing and sanding). Although at first glance copper may seem too soft for this application, it performs very well as a fill material because it has no place to go – it is confined by the indentation. Its compressive yield strength is approximately 67,000 psi., more than adequate for this application.
The entire repair was carried out in three days over the Thanksgiving Holidays and provided a total savings over the initial R&R option of nearly $75,000.
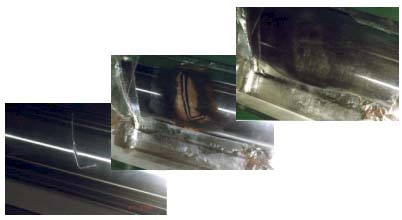
Summary
Brush plating is a valuable tool to include in your arsenal of repair equipment. It is a flexible process that offers many advantages over competitive processes such as welding and flame spray. And because it is portable, it can save both time and money!