Brush Research Manufacturing Offers Miniature Industrial Brushes For More Precise Finishes For Small Parts
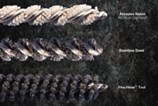
Los Angeles, CA - Brush Research Manufacturing is designing miniature finishing brushes in an array of designs and materials and in sizes as small as 0.024 in. Filament options include nylon, carbon steel, stainless steel, brass and abrasive filled nylon. The company's newest brush is filled with diamond abrasive nylon and will cut harder materials, deburr faster and last longer, providing a unique level of flexibility and longer tool life.
A miniature deburring industrial brush can solve both the productivity and quality challenges involved when manufacturing parts of various small sizes, contours and materials. These tools are generally best suited to address tight tolerances, edge blending, deburring and other finishing requirements that have a direct impact on overall functionality.
The application will certainly affect the choice of miniature brushes and includes variables such as contours required, the type of material, and the amount of material to be removed. Other factors that apply to brushes used in automated applications include RPM of the machine tool, feed rates, and the optimum wear-life of the industrial brush.
The Flex-Hone is available in miniature sizes as small as 4 mm. (0.156 in.). Sometimes referred to as the "dingleberry hone," the Flex-Hone is a ball-style flexible hone featuring globules or balls of abrasive grit permanently laminated to the end of nylon filaments.
"For applications with a bore size of 4 millimeters or greater, the Flex-Hone honing tool is almost always the preferred industrial brush," says Mike Miller, Brush Research Manufacturing. "One reason is because it's more abrasive at the point of attack, whereas an abrasive nylon brush will have abrasive grit particles interspersed throughout the filament. The ball-style honing tool is about 95 percent pure grain abrasive right at the point of need, so it really does an effective job."
Miller adds that the ball-style flexible hone is not recommended for working on threads, whereas abrasive nylon is very effective for removing burrs and polishing thread peaks and flank angles, particularly in tapped aluminum holes.
The abrasive nylon industrial brush has gained in popularity. To begin with, nylon is not reactive, Miller explains, so the brush will not impart carbon impurities onto the surface of the product. Nylon doesn't oxidize, and therefore doesn't rust or cause rust. Safety is another issue because metal filaments can develop wire fatigue over a period of time. If you are using a wire brush incorrectly, the fatigue process is accelerated.
Miller says customers with concerns about brush automation, a flexible hone, or any industrial brush application can get assistance from the Brush Research Mfg. engineering department. The company operates a surface-finishing laboratory where it analyzes customers' applications, selects the appropriate tools, and runs tests before recommending the best solution for customers.
SOURCE: Brush Research Mfg. Co.,Inc.