CleanTech 2000: Environmentally Friendly Vapor Degreaser Cleans Economically
Branson Ultrasonics Corp's Precision Processing unit (Danbury, CT) will be exhibiting the EVD-80 Ecological vapor degreaser at the show. Unlike conventional vapor degreasers, this system brings the cleaning solvent to the parts rather than the other way around. Keeping in mind the EPA, OSHA and other regulations regarding exposure of people and the environment to these vapors, the EVD-80 is sealed air-tight to keep the vapors inside the system. A wide range of solvents can be used allowing the parts to be cleaned and dried quickly.
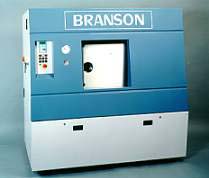
Ideal for cleaning oils, greases, chips and other soils, the EVD-80 can clean parts either in bulk or individually using vacuum distillation for on-board solvent recovery. This, along with vacuum drying, helps keep solvent loss to a minimum. The system complies with EPA and California South Coast Air Quality environment regulations on solvent emissions as well.
The EVD-80 process chamber, measuring 21- x 23-in., takes care of the whole cleaning process. This chamber can include spray manifolds and ultrasonic transducers with a power of 40 kHz if necessary and a programmable logic control function controls vapor wash, high-pressure spray wash, immersion wash with or without the ultrasonics option, fresh distillate vapor rinse and vacuum dry procedures.
The contained cleaning procedure is capable of processing up to 90 gallons of solvent in a cycle, recirculating 2 gpm at 100m. The spray manifolds located inside the chamber direct high-pressure solvent at the part(s) to be cleaned using "impingement" energy to loosen the soil and other dirt from the part(s). The vacuum pump then kicks in to dry the part and keep it dry for the duration of the cycle.
The part goes through a final vapor rinse after which the vapors pass through a heat exchanger. The heat exchanger then condenses the vapors into a liquid and returns it to the solvent recovery still where the remaining solvent molecules are "either exhausted from the machine or passed through an optional adsorption system that scrubs them from the machine," according to the manufacturer. Another option is a chiller, used to cool water, if desired.
For more information, contact Branson Ultrasonics Corporation, Precision Processing, 41 Eagle Rd., Danbury, CT 06813. Phone (800) 732-9262; Fax (203) 796-0320.