Composite Anodic Finish for Chromic Acid Anodic Finish Replacement
By Marie Pompili, using materials supplied by AESF and C.J. Saporito Plating Company
Ed. Note: The following article is based on a paper given by Jude M. Runge, Ph.D. and A.J. Pomis of the C.J. Saporito Plating Company (Cicero, IL) at the 2000 AESF Aerospace/Airline Plating & Metal Finishing Forum. Some parts of the paper are quoted directly, as indicated in the text.
Chromic acid anodizing (Type I per MIL A 8625F) was once a wonder finish, providing excellent corrosion resistance, exceptional tolerance control, and exhibiting little effect on fatigue life. However, the environmental ramifications of its use are drawing Type I finishing under fire. Type IIB thin sulfuric acid anodic films are not as corrosion and abrasion resistant as their Type I counterparts so they are not suitable replacements. The time is ripe for a replacement for Type I finishes and the folks at The C.J. Saporito Plating Company think they may have found the solution.
Possible Solutions to the Chromic Acid Dilemma
There are similarities between the aluminum anodization process and the oxidation polymerization reactions for polyaniline, which can also be made electroactive. "Because polyaniline can be made electroactive, that is, it will respond to the electrochemical processes, we can dope it in sulfuric acid and oxidatively reduce it if we anodize," Runge said in her presentation. "Because of that, we can simultaneously deposit polyaniline if we anodize it." Runge and her counterparts have since patented this process that has provided them with the means to manufacture composite anodic films for aluminum.
Runge and her team ran tests under the Mil A 8625F specification. Tests showed an increase in abrasion resistance when the new film was applied over Type II anodic films. Further, the process provided corrosion protection at all thicknesses. Encouraged by their findings, they conducted further tests to determine whether this composite anodic film would be capable of outperforming Type I anodic films.
The Experimentation Process
Runge and her team used 20 3-in x 10-in panels for comparison analysis. Ten of these panels were galvanostatically anodized with the composite at current density of 1.2 amps/dm2 for approximately 10 minutes at 70°F. The finished coating thickness was 0.00006-in (1.5µ). Another 10 panels were finished with Type I (chromic acid) finish using a potentiostatic process at 40 volts at a temperature of 96°F. Total anodizing time was 50 minutes for this procedure. The panels finished with Type I film were dichromate-sealed while the panels finished with the composite film were sealed in nickel acetate. The research team found that the "equivalent finish thickness to composite finish samples was obtained 2µ."
The research team then subjected five samples from each of the previous groups to be salt sprayed per ASTM B117. Every 24 hours they opened the test chamber doors to inspect the specimens. Each sample was subjected to the test conditions until they failed. Failure was indicated by the breakdown of the anodic film that was displayed as corrosive pits on the specimen's surface.
Traditionally, panels processed and sealed using Type I films are required to complete 336 hours of salt spray testing per Mil A 8625F specifications. The researchers observed the breakdown of Type I test panels after 288 hours of salt spray exposure while the composite finish showed no sign of pitting or other breakdown.
The team processed two additional groups of panels for comparison. Several of these panels were finished using Type I film while the remaining group was composite finished. Both groups were dyed black and were dichromate (Type I) and nickel acetate (composite) sealed. They found that while dyeing the panels black extended the corrosion resistance of the films, the samples finished using the Type I process exhibited gray streaks. The composite-finished panels exhibited no breakdown after 504 hours.
Fatigue testing was conducted, however, the results are not currently available. They will be presented at Aeromat 2000.
Conducting Microstructural Analysis
Runge and her team took one panel from each group that was finished (undyed) for the corrosion resistance testing procedure and subjected them to comparative microstructural analysis using Transmission Electron Microscopy (TEM).
The TEM found that samples finished using Type I film exhibited a random, porous microstructure made up of disordered aluminum hydroxide. They did not detect any chromium through EDS analysis, however, the instrument's detection capabilities go as low as 0.2%. Thus, if chromium was present, it was at an undetectable level. According to the paper, they found a "reaction" layer that was formed through "chemisorption" of oxygen ions during the anodization process. Measuring 25 nm, this layer probably was created as a result of the higher current density used to create the film in the first place. Because the film has a random microstructure, it helps seal the aluminum substrate and therefore keep the elements out. (See figures 1-2.)
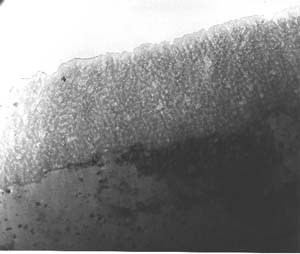
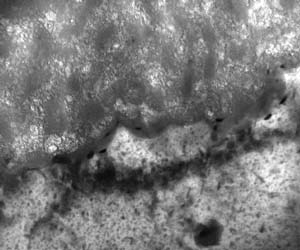
The composite film, on the other hand, exhibited a finer, more orderly structure that resembled that of Type II anodic films. The team determined that the cellular features were typical of a codeposition reaction. In addition, the reaction layer for the composite film was significantly finer than that of Type I film. This film was also corrosion resistant. However, the chemically inert polymer additive, combined with the composite reaction product that is codeposited with the film, self-seals the microstructure, according to the paper. (See figures 3-5.) In addition, scribe testing determined that the composite finish was not easily abraded and it did not expose the aluminum substrate as the Type I finish did.
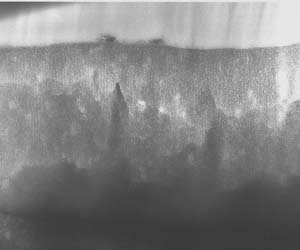
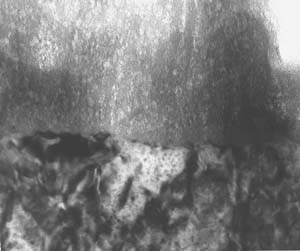
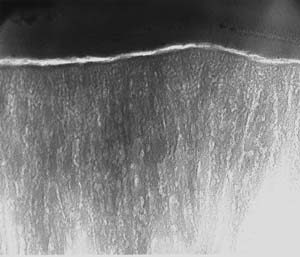
The new codeposition process, called CompCote, uses less energy than the chromic acid anodizing process. In addition, the new process can be done at ambient temperature and in a shorter amount of time than its Type I counterpart. Said Runge in her presentation, "We're actually in the anodizing bath for 10 minutes as opposed to 50 minutes to an hour for a standard chromium process. Because it was a sulfuric acid-based process, additive is essentially non-toxic at the levels we are introducing it to the formulation."
Runge and her team are further developing the CompCote process. It is commercially available in the U.S. and Europe through licensees, C.J. Saporito Plating Company and Celsius Nussbaum Oberflächentechnik in Kaufbeuren, Germany.
For more information, contact Jude Runge at C.J. Saporito Plating Co., 3119 S. Austin Ave., Cicero, IL 60804-3730. Phone (708) 222-5300; Fax (708) 780-0741.