Dry Filter Cleaning System Saves Filters and Time
By Marie Pompili
One of the basic elements of automobile maintenance is air filter replacement. The idea is that a clean filter can effectively collect dirt and prevent it from entering the engine. This same idea also goes for filters used in manufacturing. However, what many people don't realize is that replacing air filters frequently is very expensive in the long run, especially when there is a dry cleaning technology available that can clean a filter in a short period of time, leaving it with 99% efficiency for the next job.
Sonic Dry Clean, Inc., Poway, CA, developed its Sonic Dry Clean (SDC) process to fill a need for a filter cleaning process that didn't strip away every fiber of the filter after the first – and only – cleaning. Prior to the Sonic Dry Clean system, filters were either wet washed or replaced. The SDC is an easy-to-use, self-contained unit. The filter is placed inside the cabinet and rotated and vibrated to loosen dirt particles. Then, air is blown through the filter to loosen any caked on dirt and remaining debris, which is then vacuumed out. The filter moves on to finishing, and finally to an airflow check. All of this is done in less than five minutes.
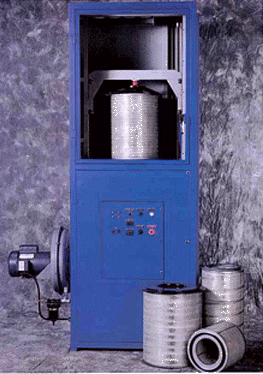
The Problem with Wet Washing
The air filter cleaning industry has been using wet washing techniques for the better part of 20 years to clean filters for multiple use. While it may seem an obvious cleaning choice, water, especially when mixed with cleaning detergents, can dissolve the specially treated paper fiber and resin composition of the filter, ultimately destroying the structural integrity of the filter. Most air filters can be wet washed one to two times before the filter media needs to be replaced. According to Sonic Dry Clean, the filter loses 20 percent or more of its filtration efficiency if it has been washed with water. In fact, some manufacturers of new filter media, including The Donaldson Company and Fleetguard, will discontinue their warranty if the filter media is washed with water because they recognize its weakening effects.
When is a Filter Actually Most Efficient?
The answer to this question is quite unexpected. "Only after five to 15 percent of the life of the filter does it become most efficient," says John Hockin, president of Sonic Dry Clean. "All filters begin life at less than 100 percent." In fact, says Hockin, "maximum efficiency is achieved when dirt is caked on." It is at this point that the filter has developed its "pre-coat," a formation of microscopic dirt particles that build up all over the filter surface producing a "light contaminant layer." This pre-coat prevents dust and other contaminants from entering an engine or other entity.
The Sonic Dry Clean Cycle
The SDC system is fully automatic and computer-controlled – the operator need only push a button and the cleaning process begins. But first, he must place a filter, ranging in size from 7" to 37" high and 3.5" to 20" OD, in the totally enclosed filter cleaning chamber. A Self-Fitting Clamping Arm locks each filter cartridge into position when the process begins. Then, the filter begins to vibrate.
During the Vibration Cycle, which lasts a total of 17 seconds, the air filter is rotated counterclockwise very slowly while strategically placed air nozzles blow controlled, compressed air inside and outside the cleaning chamber. There are three vacuum nozzles total: one located in the main cleaning chamber and two located inside and outside the filter. They work in tandem with two sets of air nozzles to clean the entire filter. The dirt is blown through in the same direction from which it came. Basically, the air nozzles blow air into the filter to dislodge dirt and the vacuum nozzles are right there to suck the dirt in and dispose of it in the system's dust collection system. Air flow through the air nozzles is directed by an air compressor of 120 cfm constant at approximately 120 psi, while the vacuum nozzles operate at about 1800 cfm at 8" water.
After 17 seconds, the vibration stops and the Clean Cycle begins. The air nozzles move to the filter's surface, adjusting to its specific surface characteristics both inside and out. The nozzles remain in the same place: one set is located on the inside of the air filter and the other on the outside. Both sets of air nozzles are designed to "mirror each other," causing the compressed air to ride the filter's media. This process removes any dirt and debris from the filter, including caked on materials. The Clean Cycle lasts about five minutes. At this point, the machine stops and releases the Self-Fitting Clamping Arm, allowing the operator to remove the filter and take it to the Finishing Table. Here, the filter is cleaned and wiped down. It then moves on to the SDC Manometer Station.
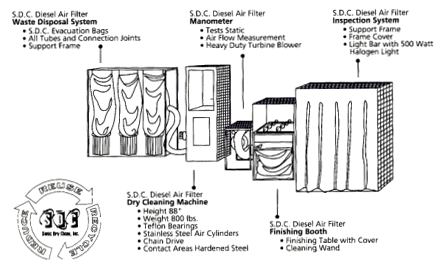
Dirty air filters are tested at the SDC Manometer Station before they are cleaned to determine the filter's airflow characteristics, i.e. does the air flow outside-in or inside-out? It also measures the amount of airflow or restriction across the filter (in inches of water) to determine the filter's operational status. The filter gasket is treated with a rubber preservative or replaced, depending on its condition. If the gasket cannot be repaired or replaced, the entire filter must be replaced.
Once the filter has passed through the Manometer Station, it visits the Inspection Station to determine its integrity. This station uses a 750-Watt Halogen Light Source and Stand to accurately inspect the filter media for any damage. Because the light source is so bright, the tiniest holes, tears, etc., can be detected.
After the entire process has been completed, the waste is removed. The waste disposal system collects the vacuumed dirt into special sealed bags for easy disposal. Another added benefit of this system is reduced waste volume.
No More New Filters
"A typical cartridge can be cleaned 10 to 15 times and some can be cleaned even more depending on the cartridge and the media," says Hockin. The SDC system returns the filter to 99.6 percent efficiency, which is better than the typical 98.6 percent efficiency realized by new filters due to its retainer of the filter's precoat during the cleaning process. In addition, the filter's structural integrity is maintained because water and chemicals play no part in the dry cleaning process.
The SDC process has been tested by various facilities and entities, including The Southwest Research Institute (San Antonio, TX), the Los Angeles County Metropolitan Transportation Authority (Los Angeles, CA) and the United States Airforce. Additionally, the system's positive effect on the environment by reducing the amount of waste deposited in landfills, has been recognized by Vice President Al Gore.
For more information, contact Sonic Dry Clean, Inc., 12170 Tech Center Drive, Poway, CA 92064-7102. Phone (800) 732-4622; Fax (619) 679-3854.