Machined Parts, Metal Burrs, And Sharp Edges: BRM Announces Deburring, Edge Blending And Surface Finishing Tools For Aircraft And Aerospace Applications
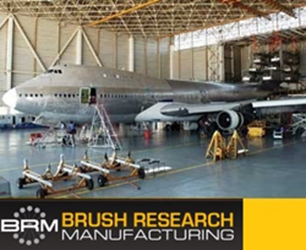
Brush Research Manufacturing (BRM), global supplier of surface finishing solutions, is announcing how Flex-Hone® technology removes burrs, blends edges, and improves surface finish for machined parts in aircraft and aerospace applications. BRM flexible honing tools also impart a plateau finish that promotes lubrication, reduces friction and wear, and helps part manufacturers meet quality requirements.
Los Angeles, CA (PRWEB) - Brush Research Manufacturing (BRM), American-owned maker of flexible hones and abrasive nylon brushes, is announcing how Flex-Hone® tools provide aircraft and aerospace manufacturers with the surface finishing solutions that they need. Ball hones, as BRM’s flexible honing tools are sometimes called, are used to remove burrs, polish holes, blend edges, and improve overall surface condition.
Surface Finishing Problems
In a recent SME article entitled Compiled Problems Caused by Burrs and Sharp Edges, a past president of the manufacturing and engineering organization described challenges faced by aerospace and aircraft companies. Burrs, sharp surface edges, and surface roughness can injure workers, cause mechanical and electrical problems, and reduce the service life of components.
Surface irregularities can also increase friction and wear, reduce fatigue limits, produce excessive stress concentrations, and create build-ups of paint and plating materials. If mating surfaces in moving parts aren’t properly finished, friction can cause excessive heat – which may lead to premature part failure. Parts also need proper finishing so that lubricants can better transfer heat away from metal surfaces.
In the aerospace industry, surface finishing challenges include chamfer blending and hole-polishing. Burr holes and sharp edges can increase stress and strain. If excessive strain occurs, material failure can result because of cracking. Aircraft and aerospace manufacturers also need to radius sharp interior and exterior corners. In industries where part failure is not an option, leaders need proven solutions.
Flex-Hone® Solutions
Brush Research Manufacturing (BRM) provides Flex-Hone® tools to aerospace companies, aircraft manufacturers, jet engine builders, and aviation MROs. A resilient, flexible honing tool with a soft cutting action, the BRM Flex-Hone® removes burrs, blends edges, and improves surface finish at the same time.
Available in a variety of sizes and abrasive types, flexible hones are also used for chamfer blending and hole-polishing. With their abrasive globules bonded to flexible nylon filaments, Flex-Hone® tools have a distinctive appearance that’s earned them nicknames such as ball hones and dingleberry hones. In the aerospace industry, however, these flexible honing tools are best known for solving surface finishing challenges.
For surface finishing hard materials, BRM recommends Diamond Flex-Hone® tools. With their resin-bonded crystals, these diamond hones are ideal for aerospace materials and space age alloys. From high-quality hole finishing at a U.S. Naval Air Station to scale cleaning at Sikorksy Helicopter, BRM flexible honing tools help keep the aerospace and aircraft industry flying high.
For more information, click here to download BRM’s Future in Finishing White Paper.
About Brush Research Manufacturing
Brush Research Manufacturing (BRM), makers of flexible honing tools and nylon abrasive brushes, is located in Los Angeles, California. For over 55 years, BRM has been solving difficult surface finishing problems with brushing technology. BRM’s Flex-Hone® tool is the industry standard against which all other surface finishing solutions are compared. Visit the BRM website to learn more.
Source: PRWeb
View original release here: http://www.prweb.com/releases/2014/04/prweb11764739.htm