Metal Corrosion Protection: One Electroactive Approach
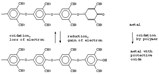
Edited by Marie Pompili with background information provided by licensing professionals in the Business Development & Licensing Department of Polymer Alloys LLC
Polymer Alloys LLC, a newly formed company with offices in Shrub Oak, NY, has recently acquired ownership of several patented/patent pending technologies from the now-terminated corporate R&D efforts of a more established company. Some of these intellectual property (IP) assets are related to the use of known polymer compositions for the corrosion protection of metal. One is a very well known polymer; the other is one that is still embryonic in its commercial development. The other IP assets deal with the use of structurally related small molecules as corrosion inhibitors; the other, an electrochemical test method for the detection of corrosion.
Polyphenylene Ether for Corrosion Protection
The first Polymer Alloys IP asset concerns the use of polyphenylene ether, (PPE), also called polyphenylene oxide, as a thin primer or wash coat treatment to corrosion protect such metals as iron, steel or copper. This PPE resin is available from GE Plastics, Asahi Chemicals and BASF Corp. It is almost exclusively used as a resin for blending with other polymers (i.e. polystyrene) for the manufacture of engineering resins with attractive properties. These include GE Plastics' NORYL, Asahi's XYRON and BASF's LURANYL products. This technology may be of interest to the metal finishing industry, in particular, since PPE resin does not contain any potentially toxic heavy metal, such as chromium.
Polymer Alloys' patented use of PPE is covered in U.S. Patent No. 6,004,628. (A full text copy of any U.S. patent listed in this article can be accessed and downloaded/printed by going to the website www.uspto.gov/patft/index.html, doing a patent number search, and clicking on the displayed hypertext link.) Pending foreign counterpart applications for this wash coat technology exist in Canada, Japan and the European Patent Office.
The as-yet-unrefined PPE technology involves the formation of a thin (e.g., about 0.2 mil or less) coating of PPE on metal that is free of any conversion coatings on its surface. The application of this wash coat is then followed by the optional, but highly preferred, application of a polymer topcoat (e.g., such as polyurethane). While some earlier, rather obscure, but patented developments by a Czechoslovakian group (J. Bures and his collaborators, specifically) indicated that PPE does not adhere to metal at all without the presence of an underlying conversion coating, the more recent Polymer Alloys work illustrates that a properly applied, thin wash coat layer of PPE has both good adhesion as well as positive corrosion protection effect for the metal. A possible mechanistic action for the PPE on the metal is as follows:
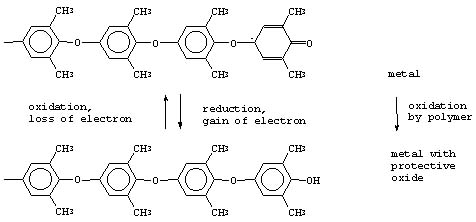
The use of a PPE wash coat is widely applicable to any metal substrate, including steel or aluminum. One of the most important potential benefits of using PPE, rather than inorganic chromates, in the initial treatment of metal substrates is the rather benign toxicological profile for PPE – it is believed to be a food-grade material for many end use applications.
Certain PPE-coated metal samples were recently tested against commercial aluminum substrates in a salt fog test (using ASTM B117, D714 and D610 test procedures). The following – and encouraging – results were obtained:
Aluminum (3003 Al) coated with ALODINE, an industry standard based on the use of chromium, showed no effect for the first four days but exhibited a few blisters (8F rating) and very slight corrosion (8a rating) at five days; another standard, 7075 T-6 Al with a MIL-C-5541 Type I Class A coating, behaved similarly. The PPE-coated 7075 Al sample at one day had 8F blistering and very slight corrosion (8a), while at five days, it showed slight corrosion (6a) and the blistering went to medium (8M) from a lower blistering configuration (8F) earlier. This was only slightly below the requirements of the industry standards and was quite encouraging – bearing in mind that the PPE wash coat formulation might be further enhanced. Two of three PPE-coated samples on 2024 Al had slight corrosion (6a) and few-to-medium blistering rating (8F and 8M) with very slight film flaking on both. The third sample completely failed at 5 days in regard to corrosion protection (0) and showed moderate film flaking – possibly due to an error in application. PPE-coated stainless steel showed very slight film flaking.
While Polymer Alloys has created a potential new market use for the well-established PPE resin, it has also created another new use for a new resin called polyaniline. Their U.S. Patent No. 5,928,795 (July 27, 1999) covers the use of the undoped (or "emeraldine base" form) of polyaniline on aluminum ("PANI-EB") as a corrosion protection agent. For a more complete report on the application of PANI-EB, see Polyaniline Coating Promises Excellent Corrosion Protection.
Rubber Antidegradents for Corrosion Protection
Polymer Alloys has also been busy with two other proprietary technology items that are also related to the polymer industry.
The first is the use of para-phenylenediamine rubber antidegradants in an organic coating (e.g., paint) for use on metal to protect the metal substrate from corrosion. (U.S. Patent No. 5,854,462 was obtained through assignment from the previous owner.)
The type of rubber antidegradants that should be selected for use in this company's approach includes those that have a p-phenylenediamine structure as their basis: -NHC6H4NH-. Aromatic amine compounds that can be utilized include various 1,4-benzenediamine and 4-aminodiphenylamine compounds, either used alone or in the form of blends. The following are particular examples of commercially available rubber antidegradants that can be selected for use:
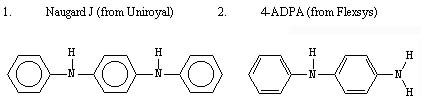
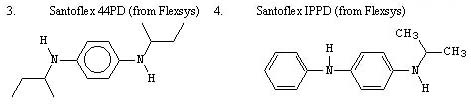
Predicting Metal Degradation
The final Polymer Alloys technology position is a patent-pending electrochemical test method for predicting the likelihood of a corrosion inhibitor-containing paint coating of metal to degrade. In this test, a painted metal sample, which has been scribed to expose metal, functions as the working electrode of an electrochemical cell. The components of such a cell include a graphite counter electrode, a saturated calomel reference electrode, and an aqueous electrolyte as shown in the following schematic:
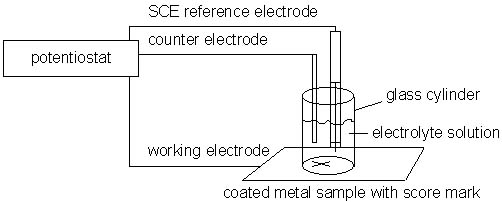
As increasingly oxidizing potentials are imposed on the working electrode by a potentiostat, the current between the working electrode and the counter electrode is measured at each applied potential. A current-voltage curve is generated which is indicative of the effects of the coating on the metal's open circuit potential and passivity. The following representative curves illustrate the use of the invention with the top curve being the DC current-voltage curves for epoxy-melamine resin, containing no corrosion inhibitive pigment, on cold rolled steel and the bottom curve being the same resin formulation containing a strontium chromate pigment:
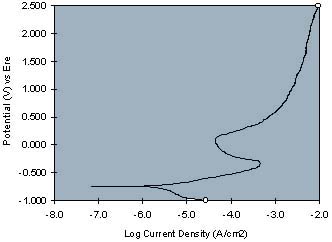
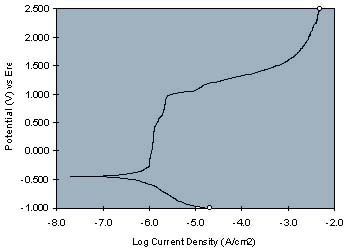
Strontium chromate's effect as a corrosion inhibiting pigment in the resinous composition is evident by a more positive open circuit potential and a more vertical current-voltage curve, as compared to the resin sample not containing a corrosion inhibitor pigment.
Polymer Alloys is interested in having any of the above further evaluated and developed for commercialization under license. Contact Polymer Alloys LLC's Licensing and Business Development Office by email at: fenquarry@aol.com; or by the following: Box 286; Shrub Oak, New York 10588; Phone (914) 962-5026; Fax (914) 962-1019.